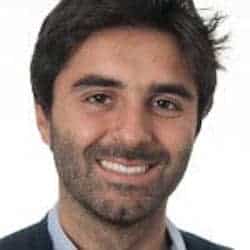
Filippo Sebastio
Gender empowerment and Equality in the Ready Made Garment (RMG) sector
A slew of industrial accidents such as the Tazreen factory fire and the recent collapse of Rana Plaza have cast the Bangladeshi garment industry in a negative light, with international media reporting extensively on the hazardous working conditions.
A fair amount of media attention has focused on the shattered lives of women employees as a result of these fatal accidents, as these women represent the backbone of the textile industry’s workforce. It remains therefore a priority that ongoing improvements of the working conditions, especially in factories used for subcontracting such as Rana Plaza, and efforts to demand fair compensation for the 2500 injured workers and the families of the more than 1100 deceased workers, occupational health and safety conditions are further strengthened.
However, the impact of industrialization on the lives of many women is often not clearly understood by international opinion. Hence, it is important to conduct a comprehensive analysis and consider what policies can actually improve the lives of the large female workforce beyond the necessary improvements with regard to occupational health and safety (OHS) such as international and national building inspections along with OHS trainings for workers and the management.
Gender Empowerment and the Garment Industry
Since the 1980s, RMG was the first industry to provide large-scale employment opportunities to women in Bangladesh, in a country where women traditionally did not work outside their home. Recent research by Professor Rachel Heath (University of Washington) and Professor Mushfiq Mobarak (The International Growth Centre and Yale University) draws attention to the significant benefits of having access to factory jobs on gender empowerment, even beyond the income opportunity, from data spanning thirty years in Bangladesh.
Comparing girls living in areas within commuting distance to a factory to both their brothers and to other girls from villages not within commuting distance, Mobarak and Heath found a systematic effect of proximity to garment factories on the postponement of marriage and childbirth age. These effects were even more striking for girls aged between 12 and 18, where early marriage is more likely to have detrimental effects on a girl’s level of educational achievement and resulting job opportunities.
Analysing retrospective data, Mobarak and Heath find that roughly 14.8 percentage points of the national gain in girls’ enrolment rates over that period, can be attributed to the growth in the garment export industry. The study also highlighted how the proximity to garment factories is associated with a reduced gender-education gap.
Such evidence sheds some light on how the RMG sector has contributed to female empowerment across and within Bangladeshi households. As factories open up and economic opportunities reach villages, households decide to invest in the education of daughters, due to the perceived increase in returns from schooling in the labour market.
Furthermore, as girls find jobs in the garment sector, they tend to postpone marriage and childbirth. Strikingly, the effect of taking up a job in the garment sector on the postponement of marriage and childbirth tends to be larger in the households where women had no previous experience of work outside of home.
Gender Equality in the Factories
Whereas a job in the RMG sector has therefore contributed to the empowerment of women who had previously been bound to work in their household, empowerment often stops when it comes to the equality of opportunities within RMG factories in Bangladesh. From data collected within factories, 4 out of every 5 production line workers are female, whilst just over 1 in 20 supervisors is a woman. If indeed workers were promoted on the basis of merit, this would mean that currently 95 percent of the managerial talent in factories emerges from 20 percent of the workforce. This begs the question as to whether it is efficient for factory owners not to invest in women, whilst the industry suffers from a scarcity of skilled workers.
Recent research has also brought to light how gender discrimination affects the lives of the female operators and the potential repercussions on the efficiency in the sector. Professors Christopher Woodruff and Rocco Macchiavello (The International Growth Centre and the University of Warwick) have evaluated a training program that trains female sewing machine operators to become line supervisors. The study investigates the impact of skill investment on female workers versus male participants and the effectiveness of female trainees who are subsequently promoted to supervisory roles. According to the study, vocational training has positive effects on gender equality as more than half of the female trainees were promoted after receiving the training.
Different experiment setups that Woodruff and Macchiavello explored suggested that after being trained, female trainees are as much or even more effective than male supervisors and that there are no differences between male and female trainees with regards to line-level efficiency, absenteeism or quality.
However, their research also draws attention to the predominant bias against women taking on the role of supervisors. Promotion rates for the female trainees in their experiment proved to be significantly lower than for male trainees and hints of resistance to the promotion of female operators were detected amongst male colleagues. Hence there is significant evidence that traditional gender roles perpetuate employment structures within factories and limits the career prospects of women entering the sector as line operators.
Three quarters of the workforce will remain unskilled without adequate training, further perpetuating a vicious cycle within factories. Due to the gender bias within factories, women do not invest in the skills required to become supervisors, as they do not expect to have opportunities for career progress. Male employees on the other hand, enter factories with a significantly higher expectation of becoming supervisors. It is not surprising then that women initially require more training en-route to becoming supervisors. With weaker career prospects, women are also likely to leave when offered better opportunities elsewhere. Consequently, garment factories face high turnover rates, leading to large costs in terms of resource and efficiency losses. A story emerges then of an industry that has fuelled economic growth in Bangladesh, yet that has been unable to exploit its full potential because gender inequality still persists.
The way forward
Mushfiq and Heath claim that the expansion of the garment industry had a far bigger role to play in increasing female educational attainment and decreasing early marriages and fertility rates during the 20-year period than most other educational policies. Mubarak and Heath’s research also shows how international boycotts on trade in garments with Bangladesh, as a response to poor and unsafe working conditions, have the potential to do more harm than good to women in Bangladesh. Since the expansion of the industry has largely contributed to the emancipation of adolescent girls, a sudden halt would put these gains at risk. This reinforces the importance of garment associations, trade unions and factory management establishing health and safety measures to ensure a safe and sustainable RMG industry.
Also, whilst it is the responsibility of government, factory owners and international brands to do everything in their power to guarantee decent and safe working conditions within the factories, more actions can be taken. In fact, international brands that outsource production to Bangladesh could also benefit from encouraging garment business associations to invest in their female operators. Bangladesh has long suffered from a negative reputation due to the working conditions in factories. By investing in social programs such as female training, international brands could together restore the deteriorated image of “Made in Bangladesh” garments and increase their appeal amongst concerned consumers.
Also, while the industry has rewarded girls that have had access to more job opportunities, factory management has failed to provide equal opportunities and the resulting career development to female workers, as compared to men. These measures would not be sustainable if garment associations and the government of Bangladesh do not work closely to change the cultural norms inside factories. Social awareness programs on traditional and social media aid in breaking down the barriers to gender equality within factories. Within garment workers’ unions, perceptions towards female workers also need to progress. Male workers need to view their female counterparts as less of a threat and more of a resource that should be highly regarded, in order to improve efficiency within this key industry in Bangladesh.
Filippo Sebastio is an International Growth Centre (IGC) economist in Bangladesh. The IGC aims to promote sustainable growth in developing countries by providing demand-led policy advice based on frontier research.